What is Porosity in Welding: Best Practices for Staying Clear Of Permeable Welds
What is Porosity in Welding: Best Practices for Staying Clear Of Permeable Welds
Blog Article
Comprehending Porosity in Welding: Discovering Causes, Impacts, and Prevention Strategies
Porosity in welding is a persistent challenge that can considerably impact the quality and honesty of welds. As specialists in the welding industry are aware, understanding the causes, effects, and avoidance methods associated with porosity is vital for accomplishing robust and trusted welds. By diving into the source of porosity, examining its harmful results on weld top quality, and exploring effective prevention approaches, welders can boost their expertise and skills to generate premium welds continually. The elaborate interaction of aspects adding to porosity calls for a thorough understanding and a proactive method to ensure effective welding end results.
Common Sources Of Porosity
Porosity in welding is primarily brought on by a mix of variables such as contamination, improper protecting, and poor gas protection throughout the welding procedure. Contamination, in the form of dirt, oil, or rust on the welding surface, develops gas pockets when heated, resulting in porosity in the weld. Inappropriate securing happens when the securing gas, commonly utilized in processes like MIG and TIG welding, is unable to completely shield the molten weld pool from responding with the bordering air, causing gas entrapment and succeeding porosity. Additionally, poor gas protection, typically due to wrong circulation rates or nozzle positioning, can leave components of the weld vulnerable, allowing porosity to create. These aspects collectively contribute to the development of gaps within the weld, weakening its honesty and possibly creating architectural concerns. Understanding and addressing these typical causes are critical action in protecting against porosity and ensuring the quality and stamina of welded joints.
Results on Weld Quality
The existence of porosity in a weld can significantly jeopardize the total high quality and stability of the bonded joint. Porosity within a weld creates gaps or tooth cavities that deteriorate the structure, making it a lot more at risk to cracking, rust, and mechanical failing. These gaps serve as anxiety concentrators, lowering the load-bearing capability of the weld and raising the likelihood of premature failing under used tension. On top of that, porosity can also work as prospective websites for hydrogen entrapment, further intensifying the deterioration of the weld's mechanical residential or commercial properties.
In addition, porosity can impede the efficiency of non-destructive screening (NDT) methods, making it testing to detect various other issues or suspensions within the weld. This can lead to considerable safety concerns, especially in vital applications where the architectural stability of the welded elements is critical.
Prevention Techniques Summary
Offered the detrimental influence of porosity on weld quality, efficient prevention techniques are essential to preserving the structural integrity of bonded joints. In addition, selecting the proper welding specifications, such as voltage, existing, and travel speed, can help minimize the threat of porosity formation. By including these avoidance methods right into welding techniques, the event of porosity can be considerably check over here minimized, leading to more powerful and a lot more reliable welded joints.
Significance of Appropriate Shielding
Appropriate shielding in welding plays a vital role in protecting against climatic contamination and making certain the honesty of bonded joints. Securing gases, such as argon, helium, or a blend of both, are commonly used to protect the weld pool from reacting with elements in the air like oxygen and nitrogen. When these reactive components enter into contact with the hot weld pool, they can cause porosity, resulting in weak welds with reduced mechanical properties.
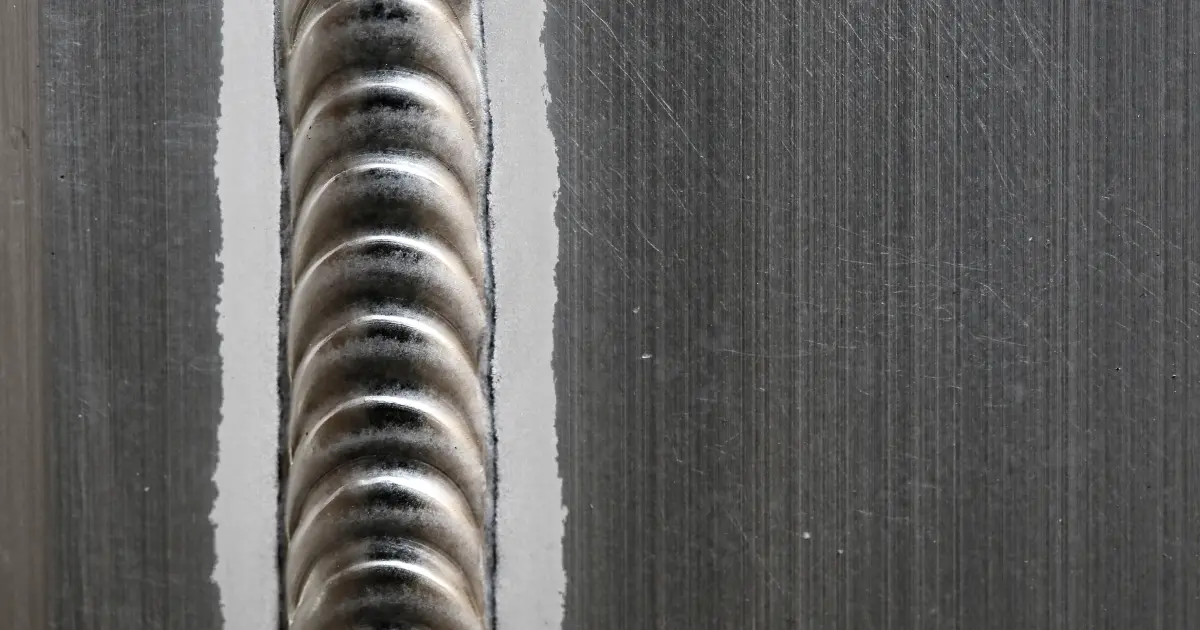
Insufficient shielding can result in different flaws like porosity, spatter, and oxidation, jeopardizing the structural honesty of the bonded joint. As a result, sticking to proper shielding practices is vital to produce high-quality welds with marginal defects and guarantee the longevity and dependability of the bonded elements (What is Porosity).
Tracking and Control Techniques
How can welders successfully monitor and manage the welding process to make sure optimum results and avoid issues like porosity? By continuously keeping track of these variables, welders can identify deviations from the ideal conditions and make prompt modifications to stop porosity development.

Furthermore, carrying out appropriate training programs for welders is important for keeping an eye on and regulating the welding procedure successfully. What is Porosity. Informing welders on the see this here value of preserving regular criteria, such as proper gas shielding and take a trip speed, can help avoid porosity concerns. Routine analyses and accreditations can likewise make sure that welders excel in surveillance and regulating welding processes
Furthermore, making use of automated welding systems can improve surveillance and control capacities. These systems can specifically regulate welding criteria, lowering the probability of human error and ensuring constant weld high quality. By combining innovative surveillance modern technologies, training programs, and automated systems, welders can properly check and read what he said regulate the welding process to reduce porosity issues and accomplish top quality welds.
Final Thought

Report this page