Comprehending What is Porosity in Welding: Causes and Solutions
Comprehending What is Porosity in Welding: Causes and Solutions
Blog Article
Porosity in Welding: Identifying Common Issues and Implementing Finest Practices for Avoidance
Porosity in welding is a pervasive problem that usually goes undetected up until it causes substantial issues with the integrity of welds. In this conversation, we will explore the vital variables adding to porosity formation, examine its detrimental impacts on weld performance, and review the ideal techniques that can be taken on to lessen porosity incident in welding processes.
Usual Root Causes Of Porosity
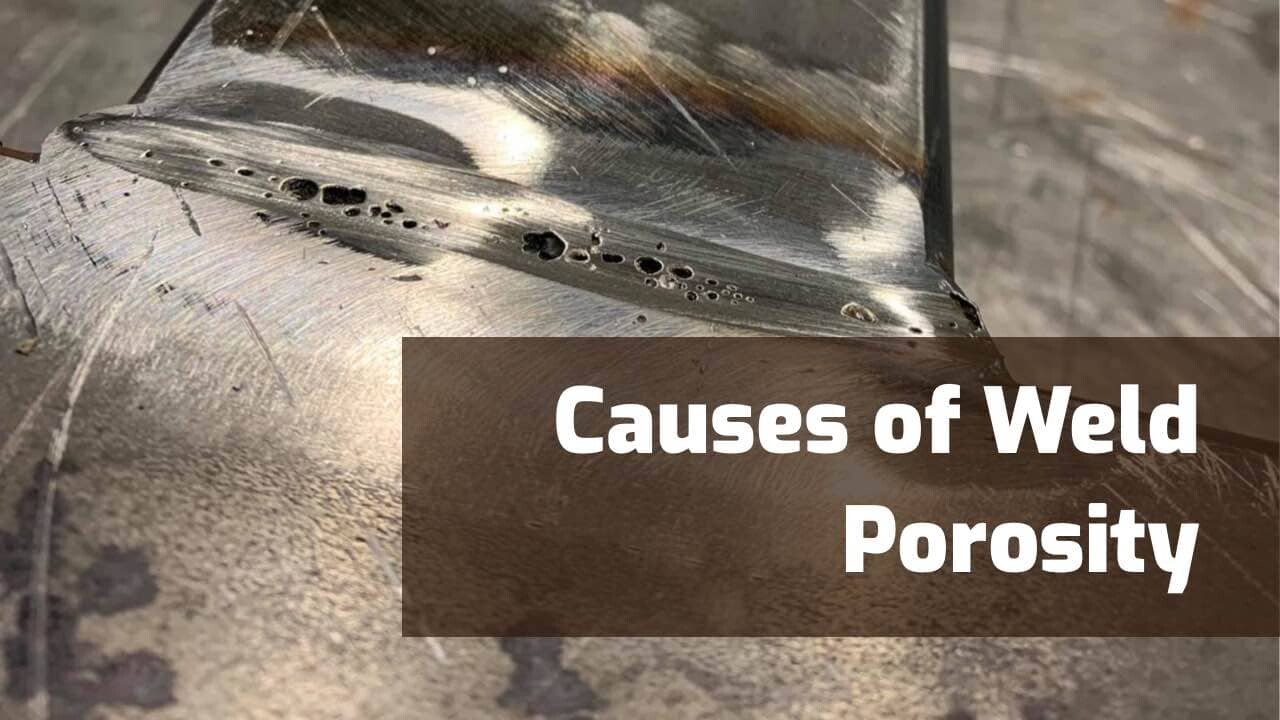
Utilizing filthy or damp filler products can introduce pollutants into the weld, contributing to porosity concerns. To reduce these typical causes of porosity, extensive cleansing of base steels, correct securing gas option, and adherence to optimal welding parameters are vital methods in attaining high-grade, porosity-free welds.
Impact of Porosity on Weld Quality

The presence of porosity in welding can substantially jeopardize the architectural stability and mechanical buildings of bonded joints. Porosity develops gaps within the weld steel, deteriorating its total stamina and load-bearing capability. These spaces function as tension concentration points, making the weld more susceptible to cracking and failing under used lots. Furthermore, porosity can decrease the weld's resistance to corrosion and other ecological factors, better lessening its long life and efficiency.
Welds with high porosity levels have a tendency to show lower influence stamina and reduced capability to flaw plastically before fracturing. Porosity can hamper the weld's ability to efficiently send forces, leading to premature weld failing visit site and possible safety dangers in essential frameworks.
Ideal Practices for Porosity Prevention
To improve the structural honesty and high quality of bonded joints, what details steps can be applied to lessen the occurrence of porosity during the welding process? Using the correct welding strategy for the specific product being bonded, such as adjusting the welding angle and gun setting, can better prevent porosity. Regular evaluation of welds and instant remediation of any type of problems determined during the welding process are important methods to avoid porosity and produce top notch welds.
Relevance of Appropriate Welding Methods
Executing proper welding strategies is extremely important in making certain the structural integrity and top quality of welded joints, constructing upon the structure of effective porosity avoidance measures. Welding strategies directly affect the total strength and durability of the bonded visit here framework. One essential facet of proper welding methods is keeping the appropriate warmth input. Excessive heat can cause increased porosity because of the entrapment of gases in the weld swimming pool. Alternatively, insufficient warm may lead to insufficient blend, developing potential powerlessness in the joint. Additionally, using the suitable welding specifications, such as voltage, present, and travel speed, is vital for accomplishing sound welds with very little porosity.
In addition, the choice of welding procedure, whether it be MIG, TIG, or stick welding, need to align with the certain needs of the project to guarantee optimum outcomes. Proper cleaning and preparation of the base steel, along with selecting the best filler material, are likewise essential components of skilled welding strategies. By sticking to these ideal practices, welders can reduce the danger of porosity formation and create high-grade, structurally audio welds.
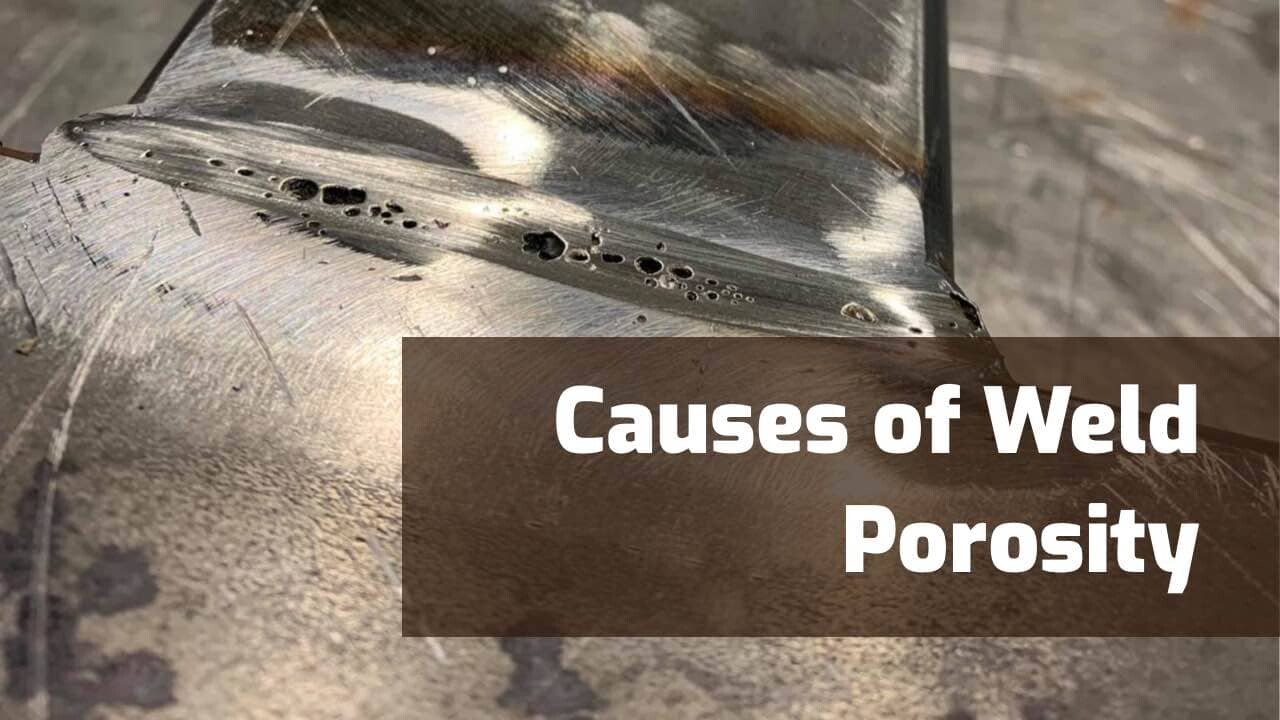
Checking and Quality Control Procedures
Checking procedures are essential to identify and stop home porosity in welding, guaranteeing the toughness and toughness of the final item. Non-destructive testing methods such as ultrasonic testing, radiographic testing, and visual inspection are generally employed to recognize potential flaws like porosity.
Post-weld inspections, on the other hand, assess the last weld for any kind of issues, consisting of porosity, and validate that it satisfies specified requirements. Executing an extensive quality control plan that consists of detailed screening procedures and evaluations is paramount to reducing porosity concerns and making certain the general high quality of welded joints.
Verdict
In final thought, porosity in welding can be a typical issue that influences the high quality of welds. By identifying the usual reasons for porosity and executing best practices for avoidance, such as proper welding strategies and screening measures, welders can make certain premium quality and reputable welds. It is vital to focus on prevention approaches to reduce the event of porosity and preserve the integrity of bonded frameworks.
Report this page